Binoculars – Manufacturing Process Review
There are brass housing covers on every binoculars model, and they are relatively heavy and expensive to produce. During the world war 1 subsequent hard rubber or leather covers were replaced in Germany by a cover of black lacquered cardboard.
The heavier brass housing covers was replaced by the galvanized steel. In the 1930s, to save brass and reduce weight, nearly all of the metal parts of the service glasses were made of aluminum.
Binocular tubes of these modern days are primarily made out of aluminum coated with silicon or a leather-like material called gutta-percha. The prisms and lenses are made from glass and have an antireflective coatings.
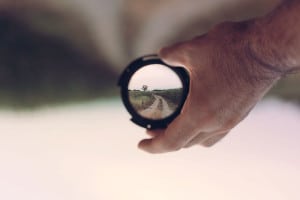
The Process Of Manufacturing
- The lens material is poured into a spherical curved bottom lens mold. The result is a lens that is about 4 inches (10.2 cm) in diameter and 1-1.5 inches (2.4-3.8 cm) thick.
- The lenses are then taken out from the molds and cut into specific pieces using a diamond saw to create optical lenses.
- They are then put into the grinding machine and polished.
- After been machined carefully, the lenses are anodized to reduce reflections in vacuum tanks. As more coatings are being applied, the lesser lights are absorbed.
- The ocular lenses (nearest the eyes) are likewise molded and carefully polished by auto-polish machines after which they are centered on a diamond turning machines and finally cleaned by running through several different solvents in automated machinery.
- The objective lenses, those furthest from the eyes, are also molded and then polished with polishing machines.
- Then manually, these components are assembled into a die cast, which is often made from aluminum.
- The optics are placed into a “plasma machine” using a technique called physical vapor deposition and coated with dielectric coatings. The coatings are essential for high performance.
- Then using lasers in specially designed particulate free rooms, the optics are then inspected and tested for clarity and defects.
- Another step is that the lasers cut the rod-shaped prisms into three-sided shapes depending on the type of prism being manufactured (i.e., porro prisms or roof prisms).
- By physical vapor deposition inside a vacuum chamber, the prisms are coated with dielectric materials (metal oxides)
- After all these components are assembled on a belt assembly line, then the collimation by hand at the final assembly station, which makes the left side exactly parallel to the right, so only one image will be seen at a time.
- A substance called gutta-percha, which looks like leather but is more durable and flexible is then used to cover the binocular housing. This covering is applied manually using adhesive and may be coated with a protective rubber covering.
- Bare metal housing are covered with plastic or rubber on the assembly line.
- The prisms are placed inside the binoculars by hand and screwed in place manually.
- With a metal or plastic ring, the objective lenses are held in place and the eyepiece is fitted with a rubber eyecap.
- The focusing lenses are placed in the housing with screws mounted by hand.
- Waterproof binoculars must be purged with nitrogen (injected through a seal), have orings at ever orifice, and sealed. Then the final step would be to pack the binoculars in cases with neck straps, most cases today being of a canvas-like material.